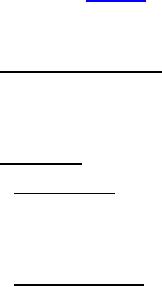
MIL-PRF-32516
fabricated into completed approved standard parts, or use of the material is approved
by the procuring activity.
k. The equipment manufacturer must have a standard commercial quality assurance
program. For example the program could be, but is not required to be certified to ISO
9001 or 9002. Other such recognized commercial quality assurance programs are
acceptable.
l. Failure criteria.
m. If required, the location of the identification plate on a transit case must be
specified.
n. The requirement for nomenclature assignment and the nomenclature to be
assigned.
o. The equipment manufacturer should have a standard Electrostatic Discharge
Control Program that complies with the requirements of MIL-STD-1686.
p. The quantity of accessories including, but not limited to: power cords, fuses (if
requited) , interface cables, etc.
q. The requirement for technical manuals (see technical manuals as defined in MIL-
PRF-28800).
r. Microsoft Windows operating system version or Non-Windows operating system.
s. The requirement for Government Validation.
t. Marking (see 3.12).
u. Number of test points per modular unit and maximum amount of test point
expansion.
6.3 First article inspection. When first article inspection is required, the equipment
should be first production units. The contracting officer should include specific instructions in
procurement documents regarding arrangements for examinations, approval of first article test
results, and disposition of first articles.
6.4 Definitions.
6.4.1 Expandability. The ability of the base equipment to be interfaced with expansion
equipment in logical increments to handle a growing amount of test points in a capable manner
or its ability to be enlarged to accommodate that growth (e.g., increments of 64, 128, 256, test
points, etc.).
6.4.2 Intermittent faults. Intermittent faults are short duration discontinuities
(opens/shorts) that occur in conductive paths in LRU/WRA chassis/ backplanes. Intermittent
faults occur as a result of various operational environmental stimuli, including, but not limited to,
thermal stress, vibrational stress, gravitational G-force loading, moisture and/or contaminant
exposure, as well as changes in the material due to age and use, such as the growth of tin
whiskers, metal migration and delamination of materials. These faults can occur individually
and /or in rapid succession on any chassis or backplane circuit. Fault durations range in time
from nanoseconds to milliseconds and have variable impedances. These circuit path disruptions
are frequently caused by: cracked solder joints; intermittent coax lines (e.g., shield corrosion,
damaged center conductor, etc.); broken, cracked or frayed wires; loose clamps; and unsoldered
pins. These circuit path disruptions often cause functional failures/faults in LRU/WRA chassis
and backplanes whose root cause(s) cannot be detected and isolated using traditional automatic
test equipment (ATE) and troubleshooting processes. Lacking the ability to detect and isolate
intermittent failures and provide environmental stimuli during test and repair process, such assets
16
For Parts Inquires submit RFQ to Parts Hangar, Inc.
© Copyright 2015 Integrated Publishing, Inc.
A Service Disabled Veteran Owned Small Business